
High altitude/low air pressure test chamber
High altitude/low air pressure test chamber
Technical parameters
Model |
MBS-QY225 |
|
Scope of application |
The equipment is intended for product reliability and performance evaluation by simulating the products in high altitude and low air pressure environment. |
|
Construction |
Size |
W (width): 700mm; H (height): 1650mm; D (depth): 1700mm (subject to inner chamber dimensions) |
Cabinet |
Double-side galvanized steel plate, with surface powder coated |
|
Inner chamber |
SUS304 stainless steel (size customizable) |
|
Inspection window |
There is an inspection window on the chamber door, with window pane being multi-layer vacuum glass. It has automatic defrosting and the film on glass surface is electronically heated to ensure no frost or condensate forms on glass surface during whichever test. |
|
Pressure bearing mode |
Inner chamber is made of quality 5mm thick SUS304 antiskid stainless steel and reinforcing U-steel is fitted around the space between inner and outer chambers to make the designed overall bearing strength exceed 10t/m. Edges of the inner wall is smooth and flat without burrs or dents, making it easy to clean and ensuring no water accumulation during operation. |
|
Technical parameters |
Display |
PLC touch screen |
|
Air pressure range |
11.6kPa-101.3kPa |
|
Air pressure fluctuation |
≤5% |
|
Vacuum degree description |
1.3kPa (at standard required simulated altitude of 15240m: 11.6kPa; vacuum gauge indicated value: 89.7kPa) Note: Since atmospheric pressure in the chamber is 101.325Kpa, in order to reduce atmospheric pressure in the chamber to 11.6kPa, you need to remove air pressure of 89.7kPa (calculated according to the standard atmospheric pressure of 101.325kPa) from the chamber, thereby achieving the low pressure environment of 11.6kPa. Now, the gauge indicates negative pressure and when it indicates the negative pressure of 89.7kPa, the low pressure of 11.6kPa is realized in the chamber. |
Technologies
Construction
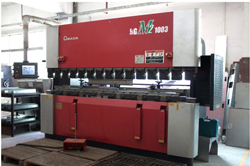

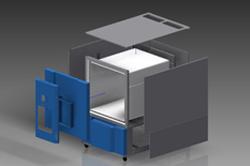
Cooling technology
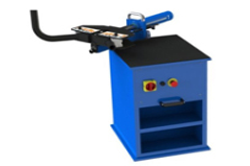
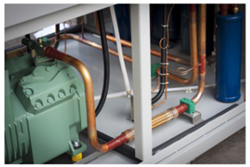
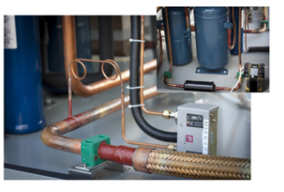
Please make sure your contact information is correct. Your message will be sent directly to the recipient(s) and will not be publicly displayed. We will never distribute or sell your personal information to third parties without your express permission.
Releted Product

Aging test chamber
MSUN series xenon-arc weathering test chamber Scope of application: It is intended for test of color fastness t...

Salt Mist Test Chamber
Applications ●Salt mist test chamber is intended for corrosion resistance test of products made of various mate...

Thermal Cycling Test Chamber
Thermal cycling (damp heat) test chamber is made of casing,inner wall,and thermal insulating material. The cooling syste...

50/60Hz Environmental Test Chamber Air Cooling 5-15°C / Minute High Efficiency
Product Presentation Three Zone Thermal Shock Chamber means the chamber consist of high temperature zone, low tempera...